Generate 200,000MW of electricity.
Invest in our people.
No weak heart shall prosper. A nation that cannot produce its own goods and commodities shall not stand the test of time.
Richard T.A. Ayoade
One of our biggest problems with production & manufacturing of goods is that we can not process our raw materials on a micro level. This means that we can not (with accuracy and precision) cut, shape & reshape, mold, join, bend, fold or build raw materials and substrates on micro level and/or scale these up on to macro level.
Mining of our natural resources on the ground and below the ground, in the air, in the sea or below the sea.
- We do not have adequate knowledge of how to mine and we have no tools to mine.
Idea conceptualization
- Because of limited available resources of the right tools needed we cannot bring conceptualization to live.
Idea development
- Even when ideas are conceptualized, because of our lack of adequate and right tools to manage knowledge, conceptualized ideas becomes difficult
to develop further and bring to live.
The little bit of our natural resources that we managed to mine (mined for us by others) were exported raw to foreign countries where they are processed and then sold back to us as finished products at exorbitant prices.
This means that we will be able to cut, shape & reshape, mold, join, bend, fold or build with accuracy and precision all mechanical, technical and common materials used to make manufactured goods such as iron, steel and other metals, plastic, glass, porcelain, ceramics, woods and planks, stone block and concrete, leather, etc.
For Simplicity sake, for us to manufacture a computer for example, let's say a desktop computer (the same principle will apply to a laptop computer or any manufactured product).
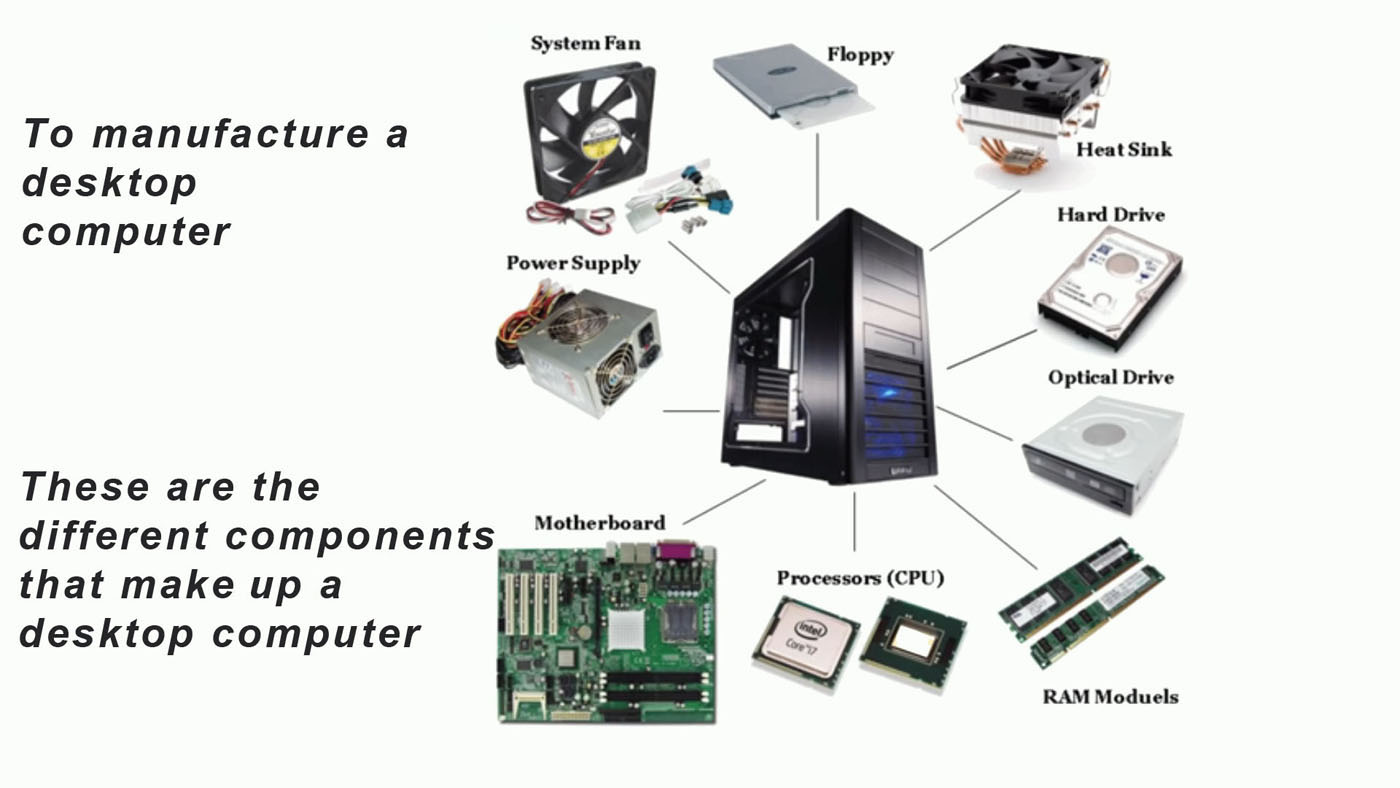
If we categorize the eight component groups into three manufacturing categories (as below) namely:
Category A (internal structure, external structure, body frame and other components made up of mainly plastics, metals, etc)
Category B (All electronic components like wire cables, amplifier, transistor, transformer, mother board, cpu, memory module, hard disk, power supply components, etc)
Category C (All required software for the operating system, the mother board, the cpu, the ram, the rom, cooling, etc)
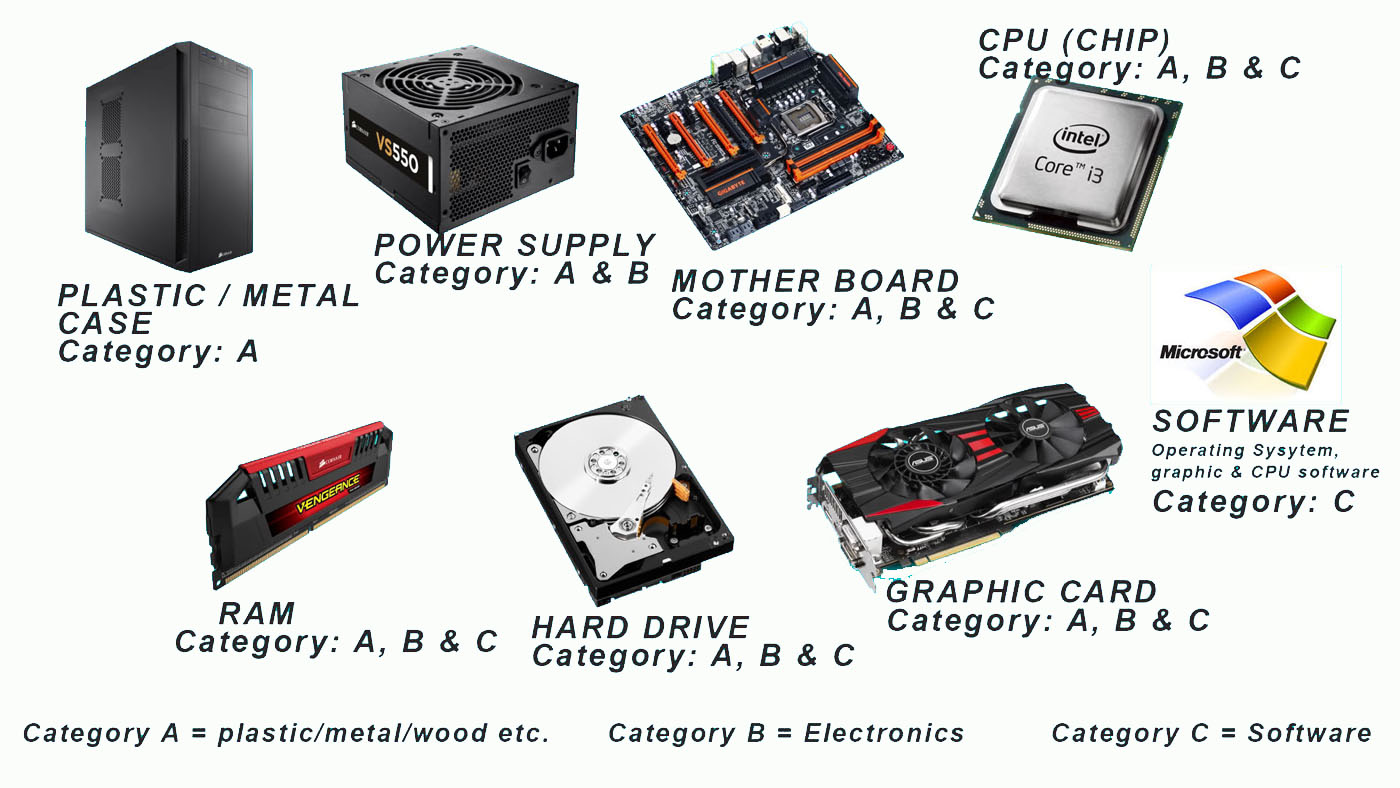
- Subtractive Manufacturing Technology
- Additive Manufacturing Technology
- Injection molding Manufacturing Technology
- Casting Manufacturing Technology
At the core of our manufacturing technologies will be the deployment of a modern manufacturing applied technology known as COMPUTER NUMERICAL CONTROL TECHNOLOGY
COMPUTER NUMERICAL CONTROL machines combine a motorized maneuverable tool (e.g saw and drills) and often a motorized maneuverable platform, which are both controlled by a computer core, according to specific input instructions.
Instructions are delivered to a COMPUTER NUMERICAL CONTROL machine in the form of graphical computer-aided design files, which are transformed into a sequential program of machine control instructions, and then executed.
- Subtractive manufacturing is when 3D objects are constructed by successively chipping and cutting material away from a solid block of material. Subtractive manufacturing can be done by manually cutting the material but is most typically done with a CNC Machine. Advanced CNC machines utilize multiple tools and cut around at least three (x, y, and z) axes such that they minimize the requirement for designers to flip the block.
One of the principal advantages to subtractive manufacturing is for example the ability to machine (with accuracy and precision) an extremely thin piece of plastic into a living hinge. For those prototypes that require living hinge components it is useful to produce certain parts using additive manufacturing while using the CNC machine for specialty components like a living hinge.
KETA will bring the knowledge to manufacture every single component (including the software) of the needed COMPUTER NUMERICAL CONTROL machines.
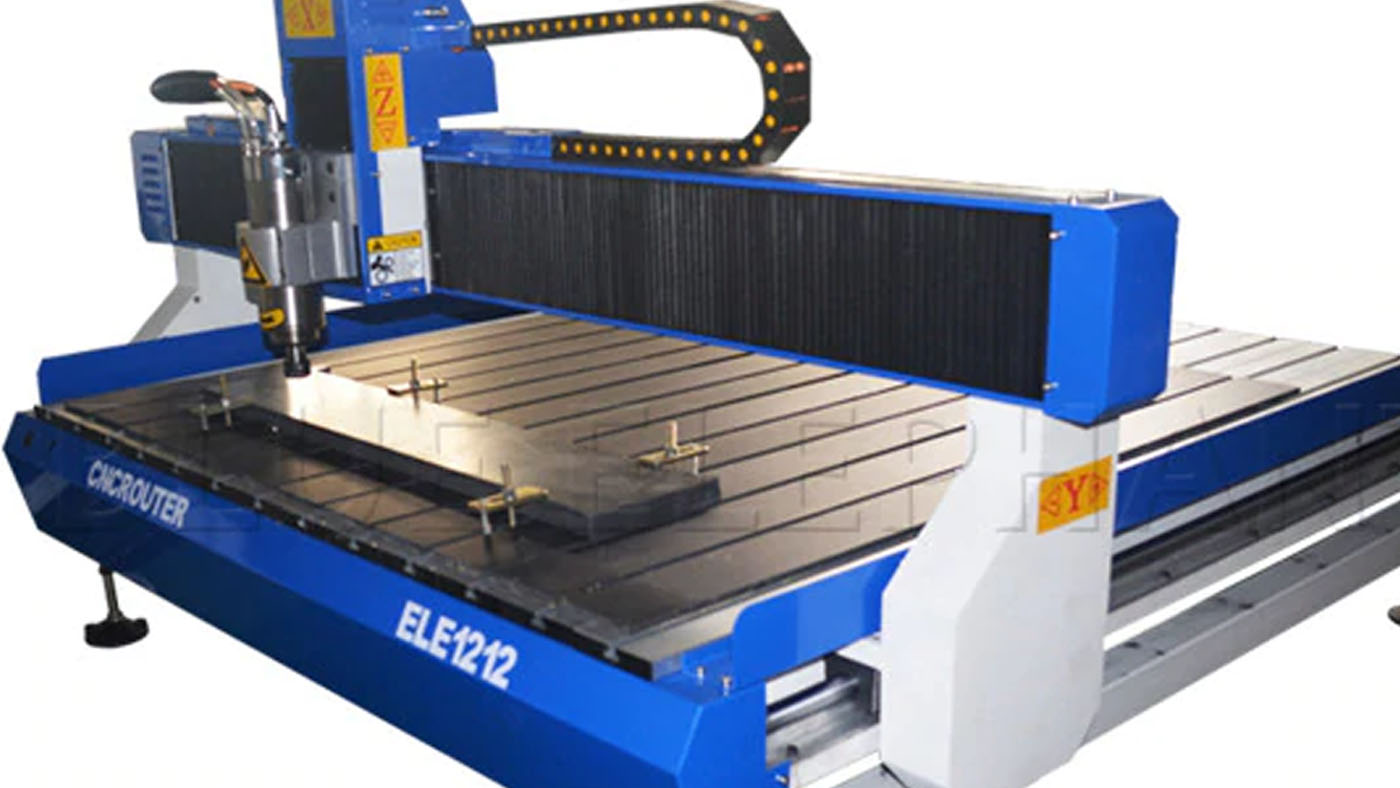
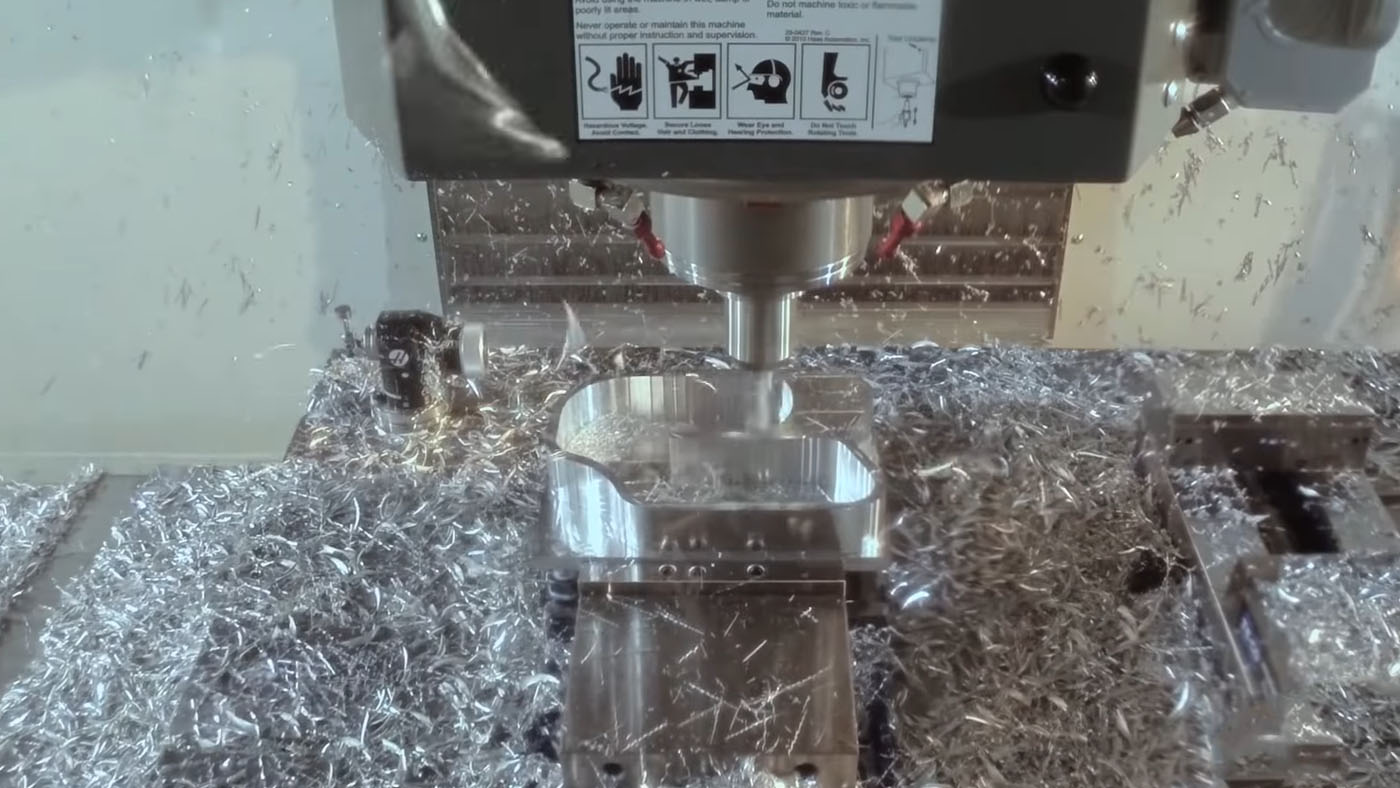
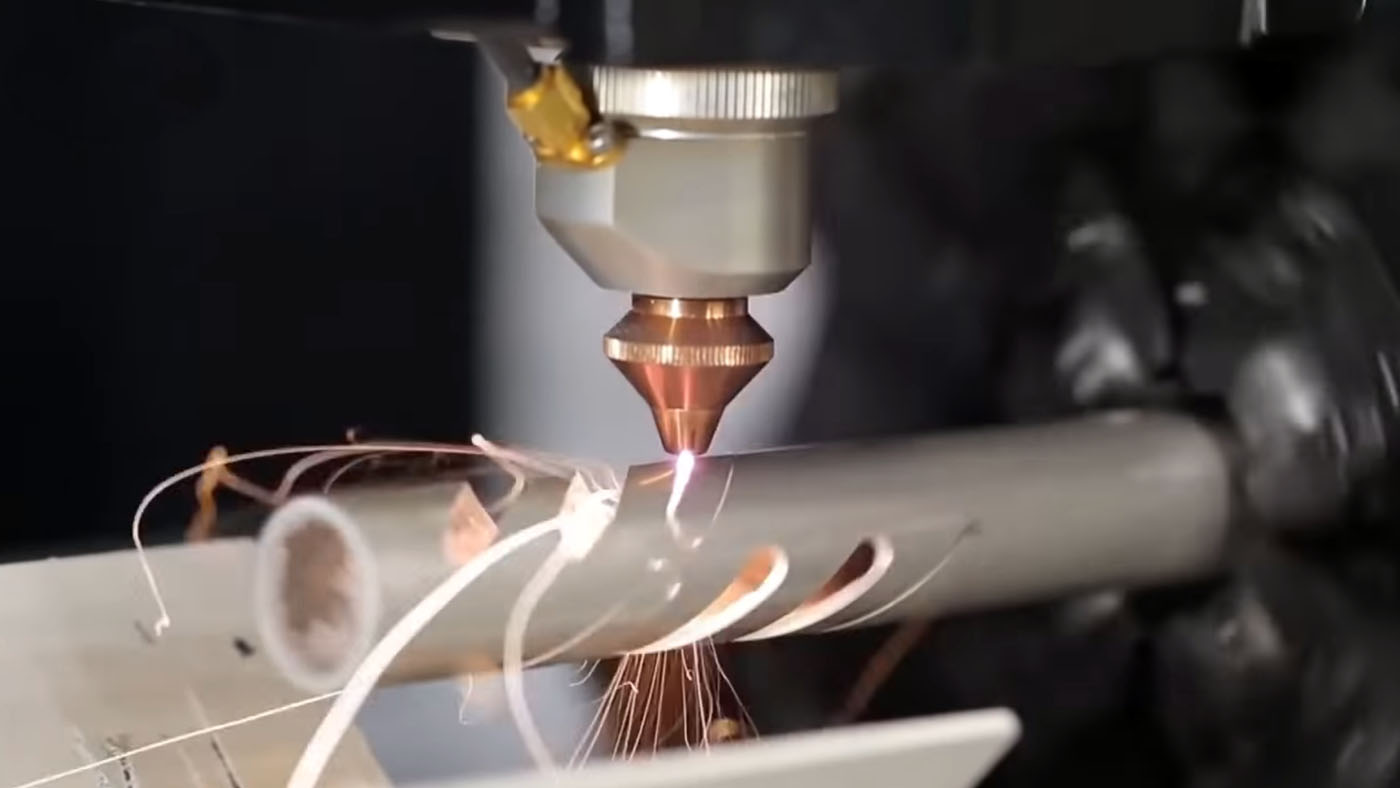
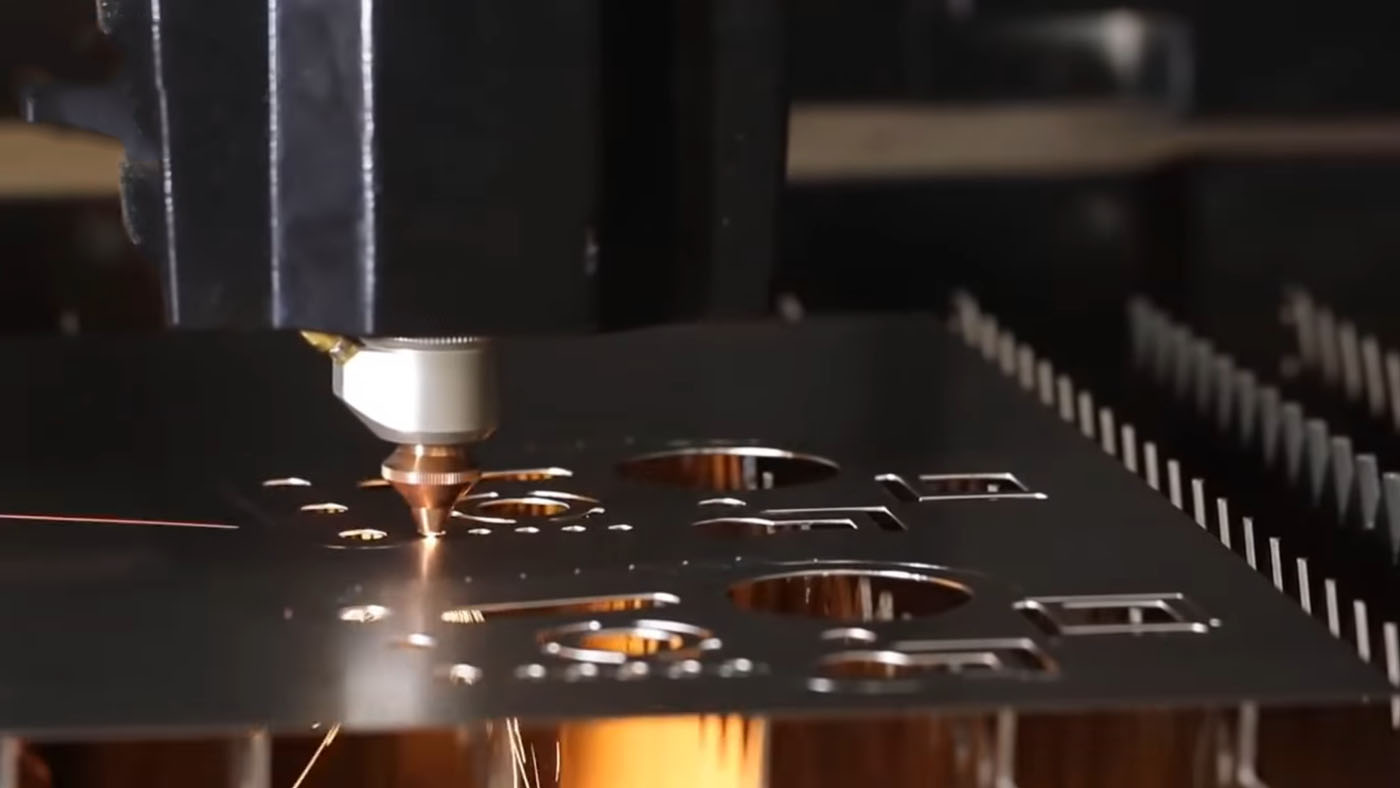
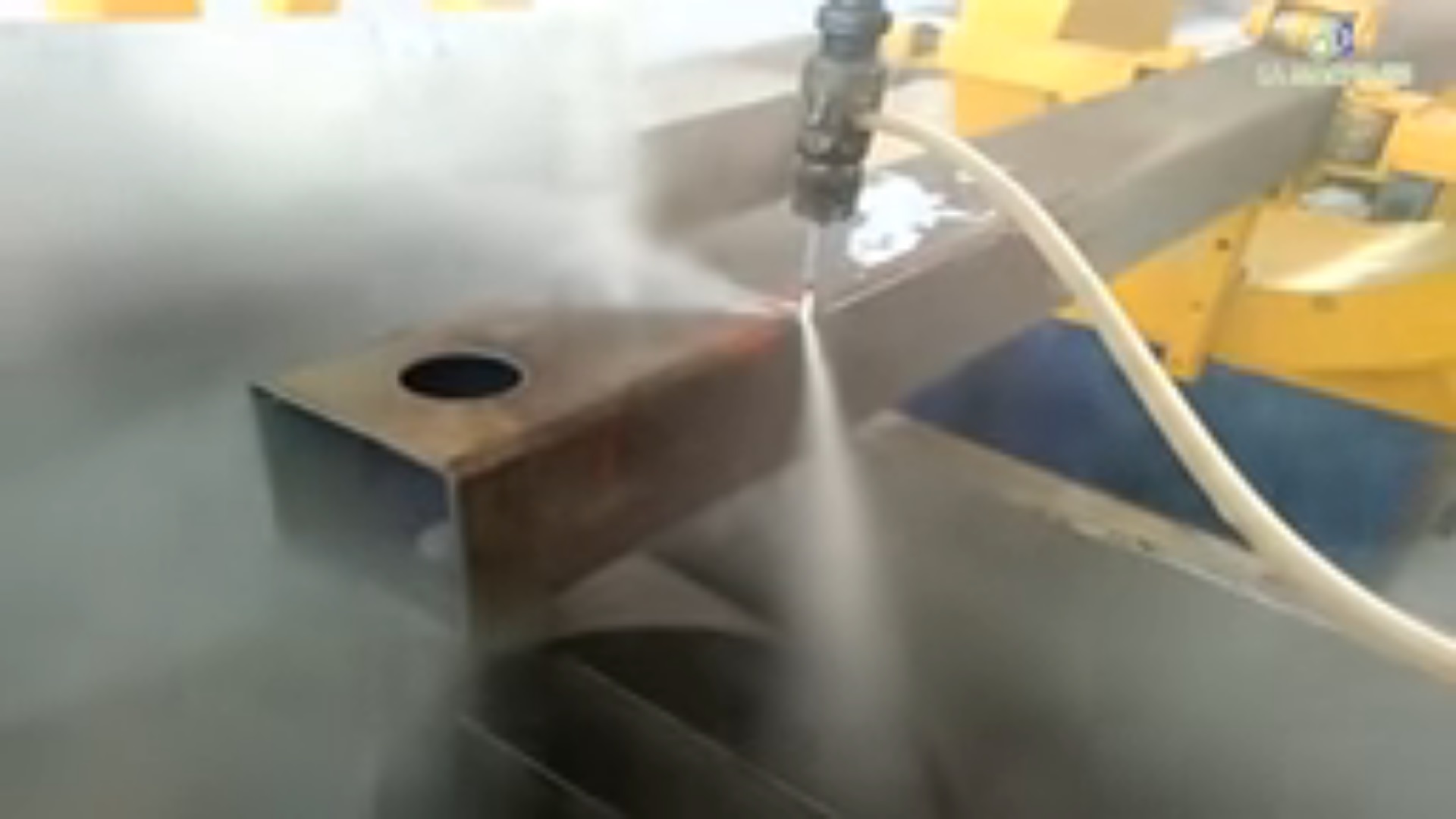
LATHE MACHINE is the undisputed king of milling metals, KETA will also bring the knowledge to manufacture every single component of Lathe machine
and KETA will even deploy COMPUTER NUMERICAL CONTROL TECHNOLOGY into Lathe machine in order to enhance its automation.
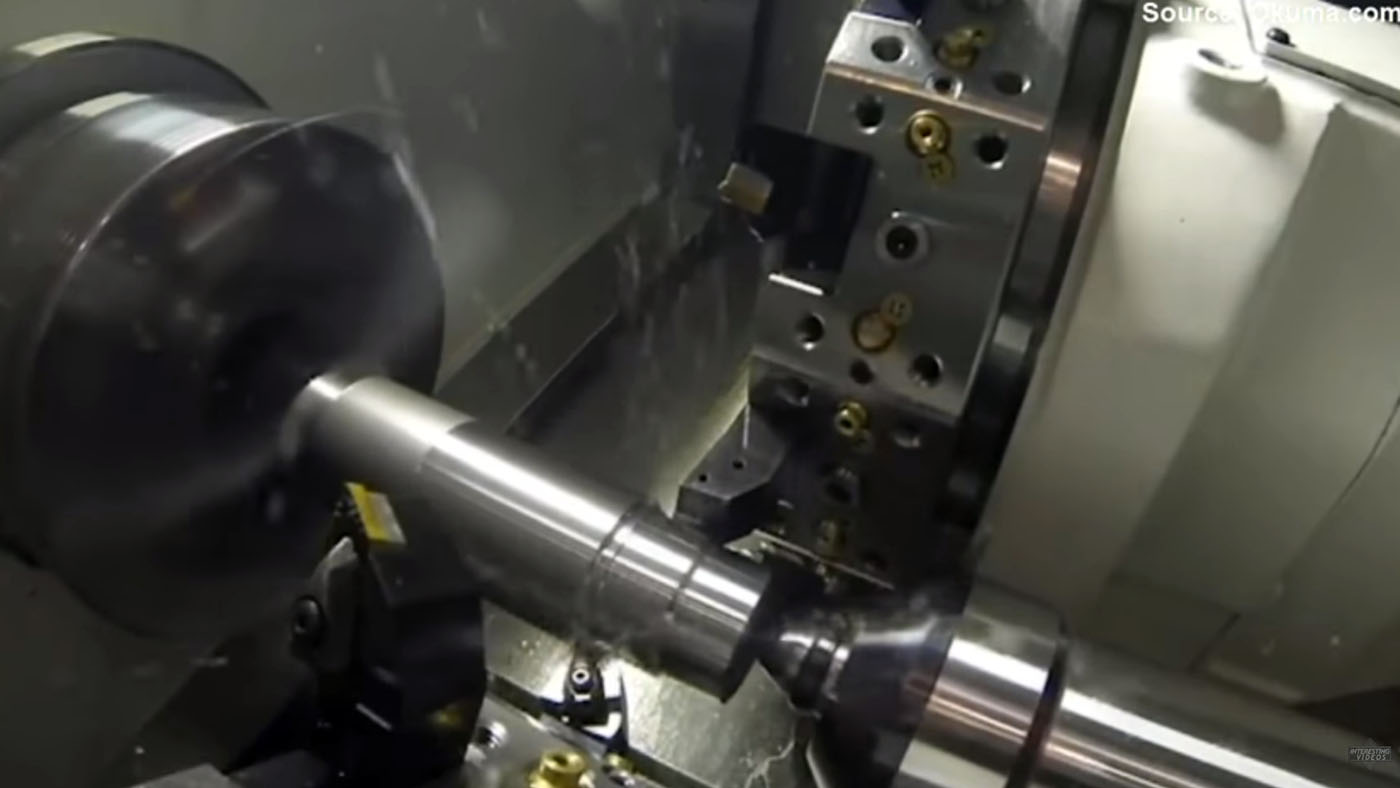
Extreme Ultraviolet Lithography (EUVL) is the most modern of subtractive manufacturing technology. From using UV lights with a wavelength of 193nm to 13.5nm, and now to 7nm, the world semi-conductor industry is pushing fast towards making even faster and more powerful computer chips. The emphasis here are on speed, accuracy, precision and down scalability. While the work on this is still patented (wavelength at 7nm going to 5nm) there are other technics to achieve this extremely low wavelength to etching patterns on semi-conductor computer chip wafers (e.g electron-beam lithography (EBL) machine).
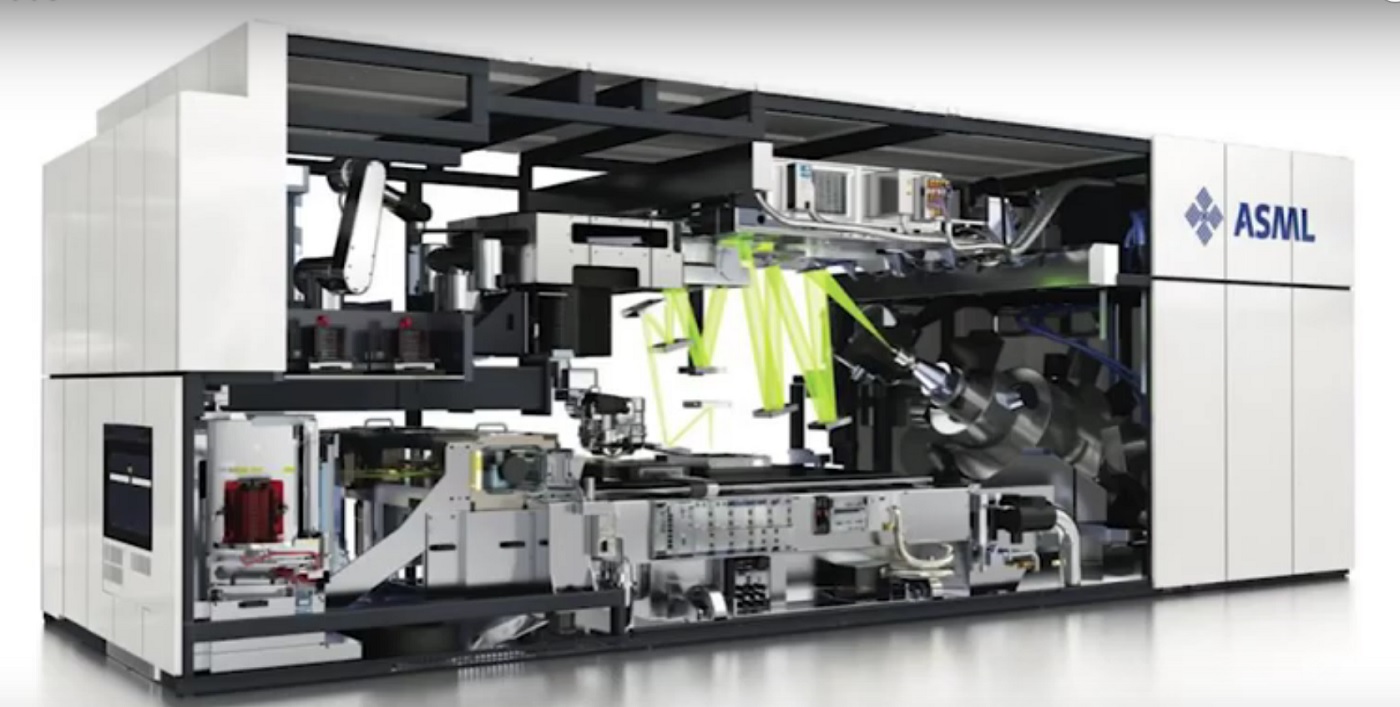
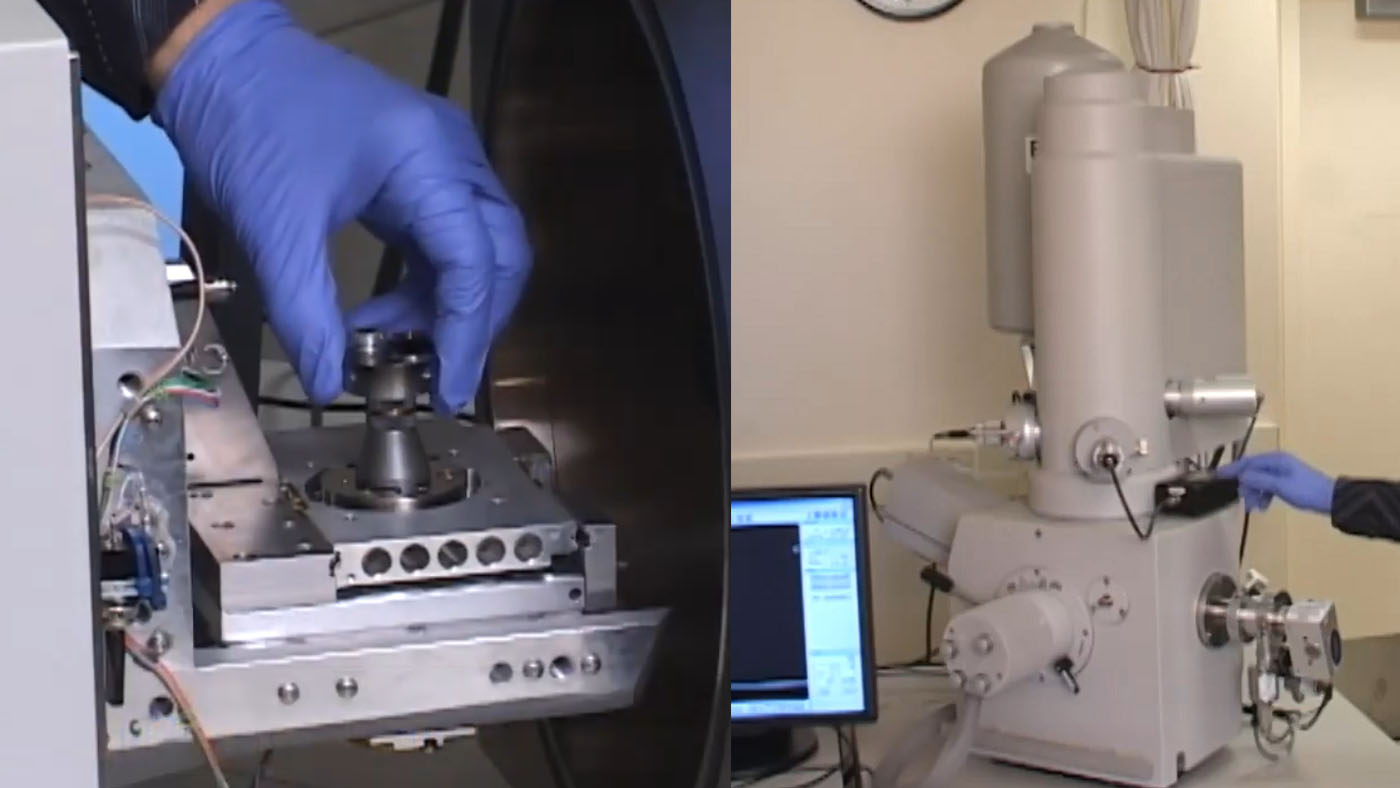
Electrical Discharge Machining (EDM) is a metal fabrication technique whereby electrical discharges are used to shape metal substrates to a desired form and shape. High voltage arc electric charges are used to chip away minutely at metal part till predesigned shape and form are achieved. This form of fabrication is used for high precision cutting of both soft and really hard metals (including hardened steel) and for fabrication of complex shapes and forms. This subtractive form of manufacturing is also commonly used in "die" piece fabrication, the most important metal piece in die casting technology.
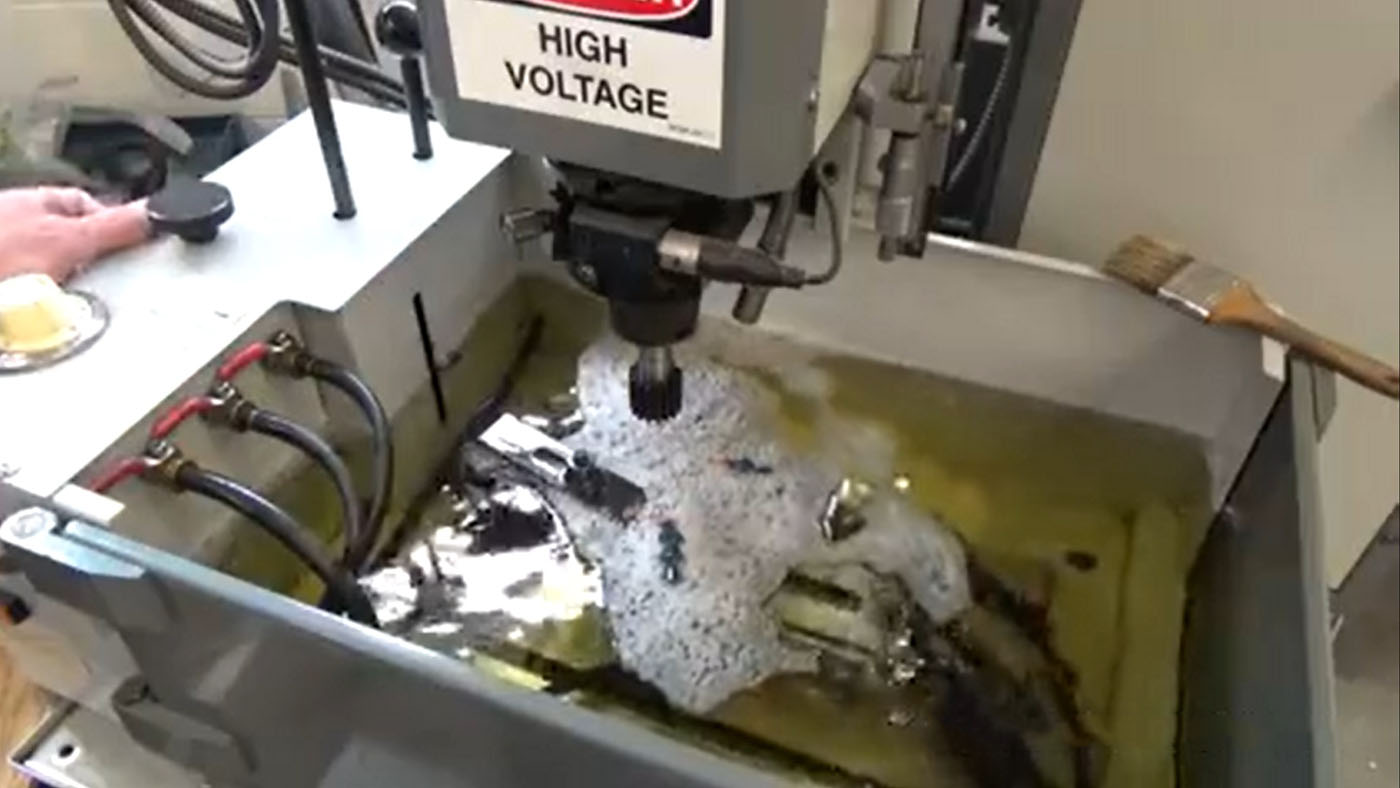
COMPUTER NUMERICAL CONTROL is a major advance in machining, and is a vast improvement over non-computer type machining that requires manual control, by hand wheels or levers, or mechanical control by fabricated pattern guides. In COMPUTER NUMERICAL CONTROL systems, the design of a mechanical part and its manufacturing program can be highly automated.
In COMPUTER NUMERICAL CONTROL TECHNOLOGY, motion is controlled along single and multiple axes, (that is X axis or X and Y axes, and can be as many as six axes), and a tool spindle that moves in the Z axiz (depth). The position of the tool (on the X, Y, U and Z axes) or the movement of material along any axis is driven by direct-drive micro-stepper motors or servo motors in order to provide highly accurate and precise movements.
Open-loop control for non-commercial use of COMPUTER NUMERICAL CONTROL machines (micro-stepper motor) will ensure adequate speeds so that accuracy and precision do not suffer. On commercial COMPUTER NUMERICAL CONTROL machines and servo motors CNC (e.g. metalworking machines) closed loop controls are required in order to provide the accuracy, speed, and repeatability.
Once an idea is conceptualized, this idea will need to be drawn out in a 3D computer software called COMPUTER-AIDED DIAGRAM (CAD). In this software
the mechanical dimensions of the part to be manufactured will be defined and drawn out in 3D.
The 3D image created in COMPUTER-AIDED DIAGRAM (CAD) is then translated into a manufacturing directives by another computer application called COMPUTER-AIDED MANUFACTURING (CAM) software.
After this, the resulting directives from CAM are transformed by a CNC controller and a CNC shield hardware such as Arduino UNO and a "post processor" manufacturing software such as GRBL into the specific commands (G-codes and M-codes) necessary for a particular machine to produce the component, and then these codes are loaded into the COMPUTER NUMERICAL CONTROL machine.
The versatality, applicability and useability of COMPUTER NUMERICAL CONTROL technology is almost limitless. KETA will deploy this technology (often with additional safety interlocks) in 3D printers, tape and fiber placement, routing, picking and placing, sawing, milling, welding, friction stir welding, ultrasonic welding, bending, spinning, hole-punching, pinning, gluing, fabric cutting, sewing, laser cutting, flame and plasma cutting, waterjet cutting and many more.
- Additive Manufacturing is any process by which 3D objects are constructed by successively depositing material in layers such that it becomes a predesigned shape. This is the technology used in 3D printers. Modern 3D printing has always been very useful for rapid prototype development but it is starting to make its impact on the manufacturing world as well. Latest developments in 3D Metal manufacturing technology includes 3D metal printing machines, Directed Energy Deposition (DED manufacturing), Electrochemical priting additive manufacturing (localized EDM), etc
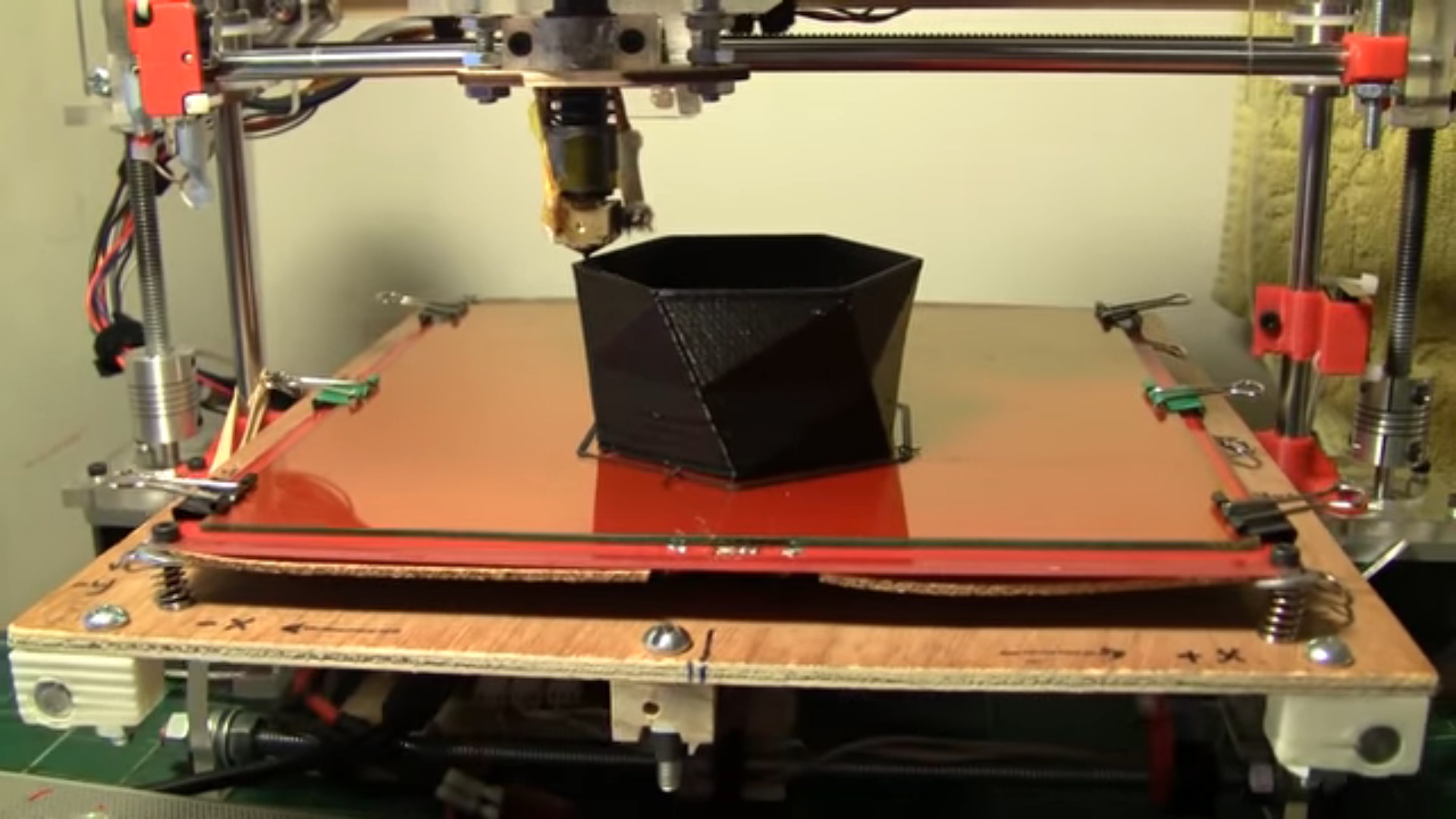
KETA will deploy the following Additive Manufacturing techincs:
Stereolithography (SLA): This is a form of 3D printing technology used for creating models, prototypes, patterns, and production parts in a layer by layer fashion using photopolymerization, a process by which light causes chains of molecules to link, forming polymers. This manufacturing process is only applicable to acrylic/plastic manufacturing.
Selective Laser Sintering (SLS): This involves the use of a high power laser (for example, a carbon dioxide laser) to fuse small particles of plastic, metal, ceramic, or glass powders into a mass that has a desired three-dimensional shape. The laser selectively fuses powdered material by scanning cross-sections generated from a 3-D digital description of the part (for example from a CAD/CAM file or scan data) on the surface of a powder bed. After each cross-section is scanned, the powder bed is lowered by one layer thickness, a new layer of material is applied on top, and the process is repeated until the part is completed.
Because finished part density depends on peak laser power, rather than laser duration, an SLS machine typically uses a pulsed laser. The SLS machine preheats the bulk powder material in the powder bed somewhat below its melting point, to make it easier for the laser to raise the temperature of the selected regions the rest of the way to the melting point. This manufacturing process is suitable for the manufacturing of plastic, ceramic, glass, etc.
Direct Metal Laser Sintering Manufacturing (DMLS) : With selective laser melting, thin layers of atomized fine metal powder are evenly distributed using a coating mechanism onto a substrate plate, usually metal, that is fastened to an indexing table that moves in the vertical (Z) axis. This takes place inside a chamber containing a tightly controlled atmosphere of inert gas, either argon or nitrogen at oxygen levels below 500 parts per million. Once each layer has been distributed, each 2D slice of the part geometry is fused by selectively melting the powder.
This is accomplished with a high-power laser beam, usually an ytterbium fiber laser with hundreds of watts. The laser beam is directed in the X and Y directions with two high frequency scanning mirrors. The laser energy is intense enough to permit full melting (welding) of the particles to form solid metal. The process is repeated layer after layer until the part is complete.
The DMLS machine uses a high-powered 200 watt Yb-fiber optic laser. Inside the build chamber area, there is a material dispensing platform and a build platform along with a re-coater blade used to move new powder over the build platform. The technology fuses metal powder into a solid part by melting it locally using the focused laser beam. Parts are built up additively layer by layer, typically using layers 20 micrometers thick. This manufacturing process is also suitable for the manufacturing of plastic, metal, glass, etc.
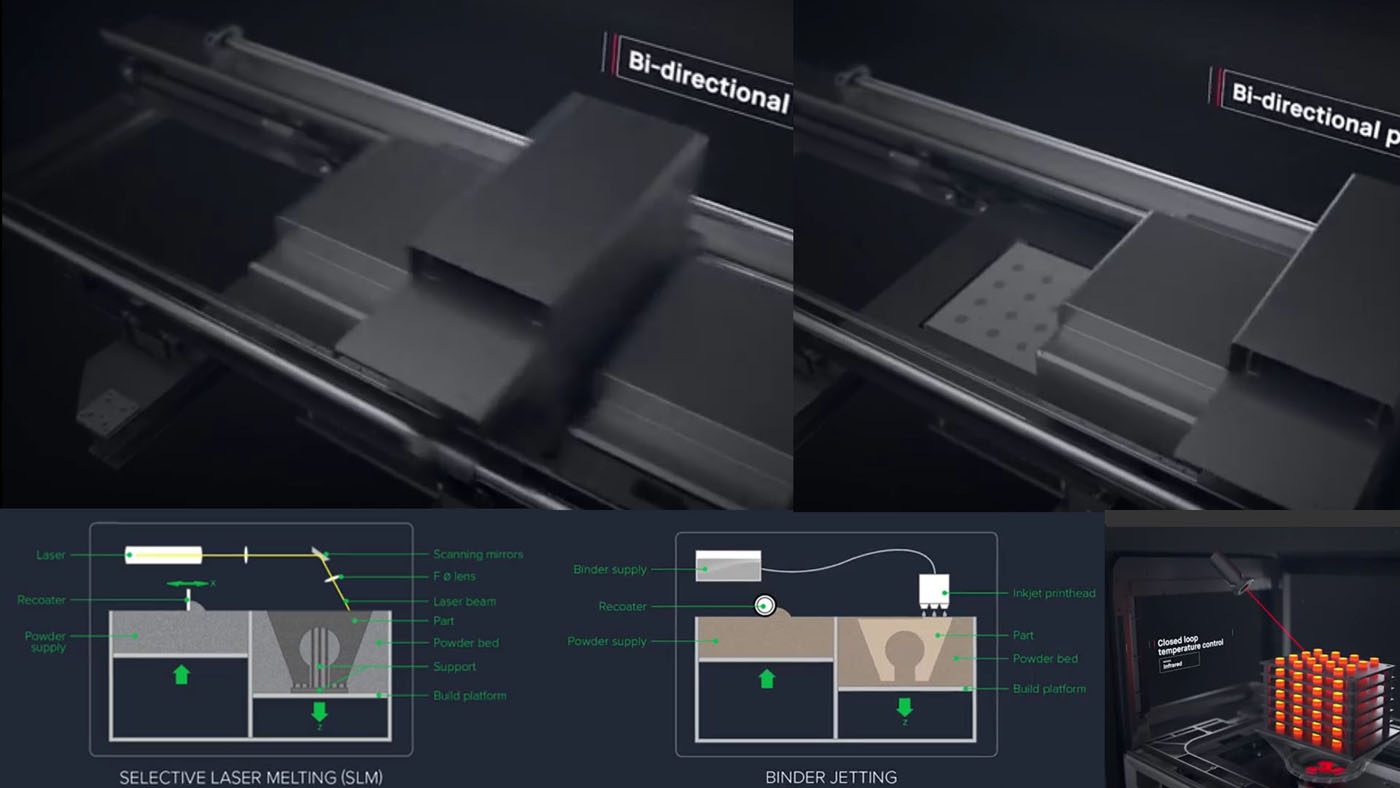
- Injection Molding Manufacturing Technic is a technic that requires the use of a mold to cast the required part. The mold is reusable for producing
the manufactured part over and over again. The mold is sometimes referred to as the "die" that is "master copy" from which
many copies will be manufactured. Thus it is the king of mass production.
This can be an effective technology for pre-production prototypes but generally it’s used for final manufacturing. Building a pre-production injection molding tool/machine is expensive, so unless you were planning to mass-manufacture a product or unless you needed to produce a moderate quantity (300-1000) of prototype parts for consumer testing and market research prior to mass-production then it not a viable option. The advantage to injection molding is that you can manufacture your prototype (or final) part in the final material.
It is also much more efficient in terms of time to use injection molding when you’re creating more than several dozen copies of a product. Costs are generally much higher when using an injection molding machine but once you generate several hundred copies the economy of scale kicks in. Although this manufacturing process is suitable for the manufacturing of plastic, metal, glass, etc, it requires extra manufacturing processes like "metal sintering" and extra part milling might be required when manufacturing very hard materials, substrates and parts like metal, steel,ceramic, etc.
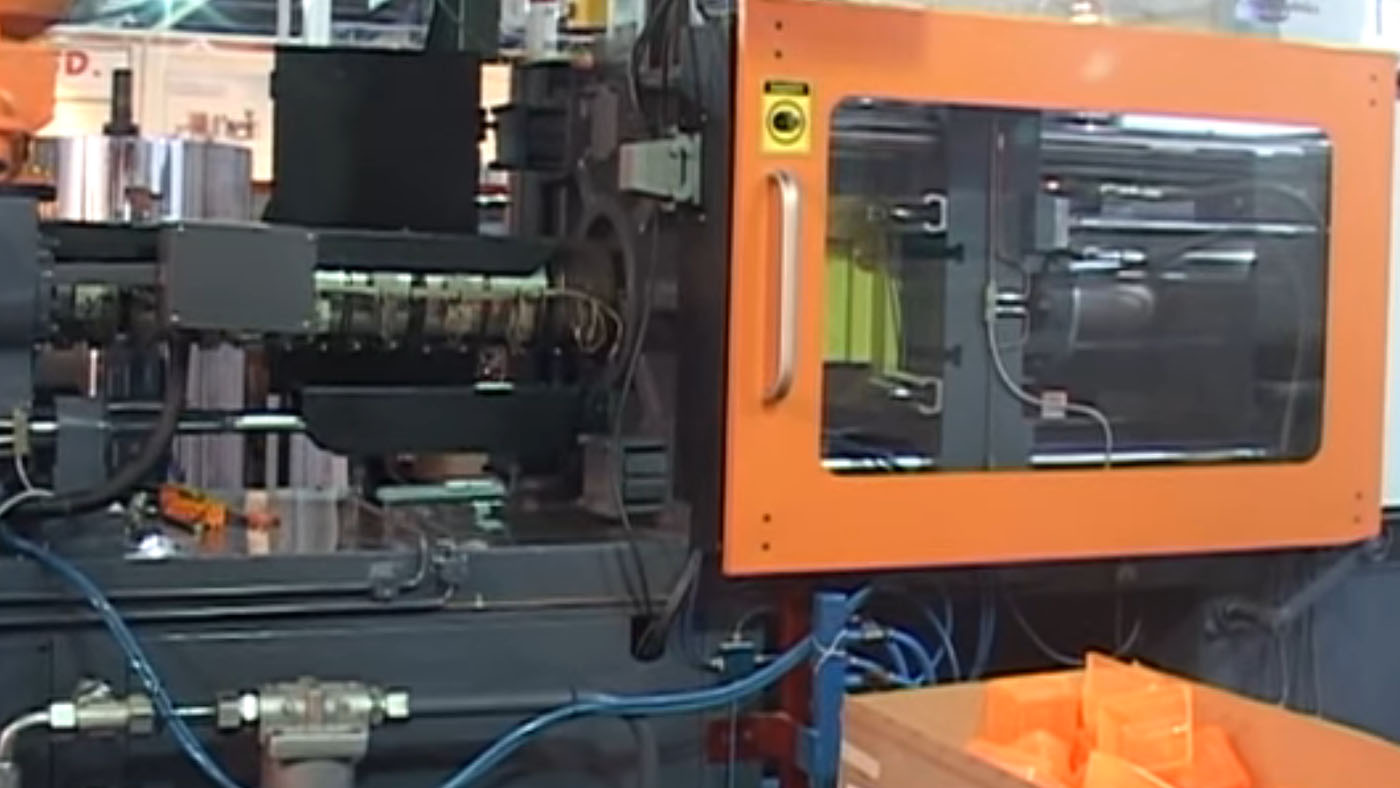
- Casting Manufacturing Technic will be one of the most important of our manufacturing technics. This is because compared to other technics,
it is a cheap form of manufaturing both small and large metal parts. Thus, it is excellent for manufacturing large pieces needed in the construction industries.
All castings require molds. But there are different casting technics. And mold can either be expendable mold or non-expendable mold. Expendable mold casting includes sand casting, loam casting, investment casting, evaporative casting, etc. Non-expendable mold casting includes die casting, continous casting, centrifugal casting, etc. Most casting technics are geared to casting specific metal alloys based on their alloy composition, heat tolerance, melting point, ferrousity, etc.
Materials used for making mold can be ceramic, steel metal or sand. And different methods are used for filling mold with the material to be casted.
Sand casting or Sand molded casting is a metal casting process characterized by using sand as the mold material.
The term "sand casting" can also refer to an object produced via the sand casting process. Sand castings are produced in specialized factories called foundries. Over 60% of all metal castings in the world are produced via sand casting process.
Your casting or end product can only be as good as your mold!. And yet molds made from sand are relatively cheap, and sufficiently refractory even for steel foundry use. In addition to the sand, a suitable bonding agent (usually clay) is mixed or occurs with the sand. The mixture is moistened, typically with water or oil, but sometimes with other substances, to develop the strength and plasticity of the clay and to make the aggregate suitable for molding. The sand is typically contained in a system of frames or mold boxes known as a flask. The mold cavities and gate system are created by compacting the sand around models called patterns, by carving directly into the sand, or by using a 3D printed object.
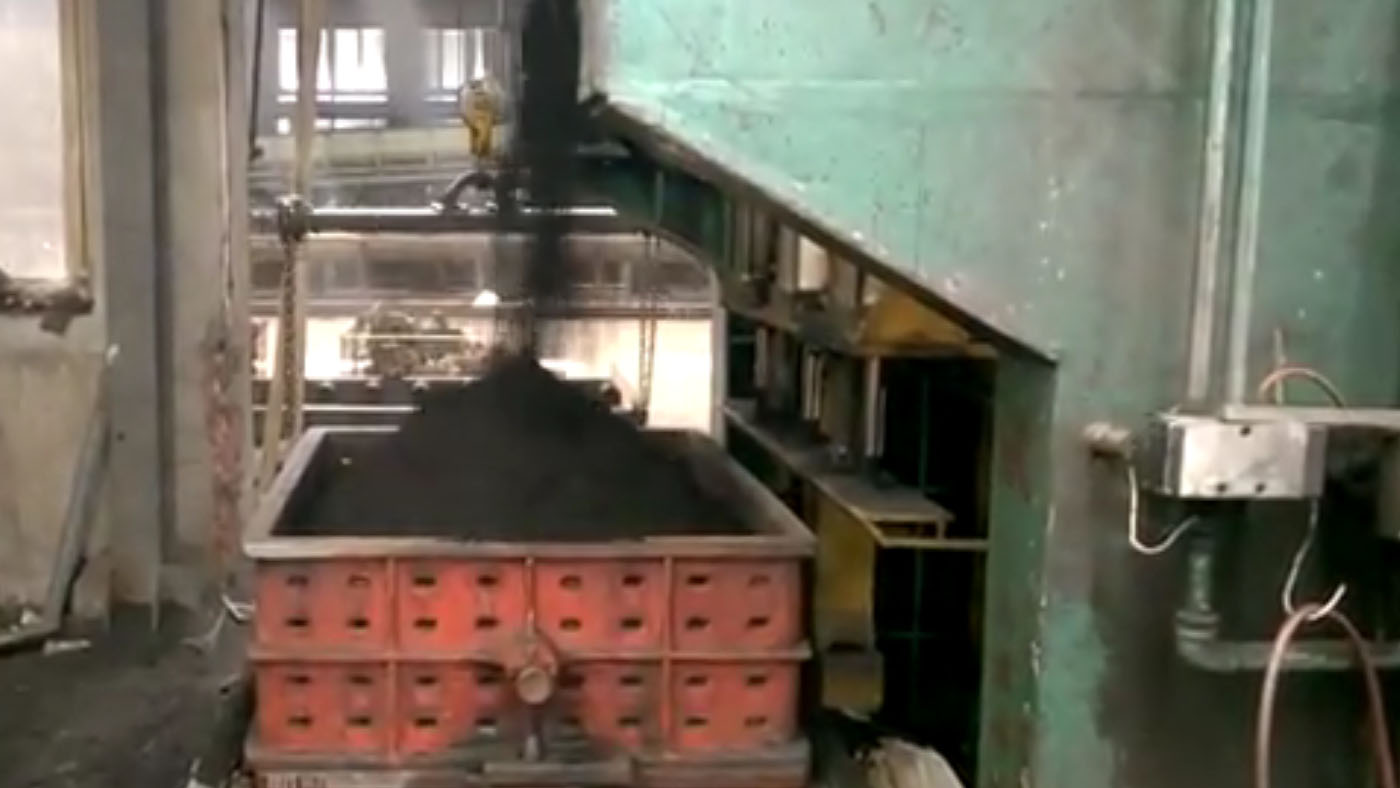
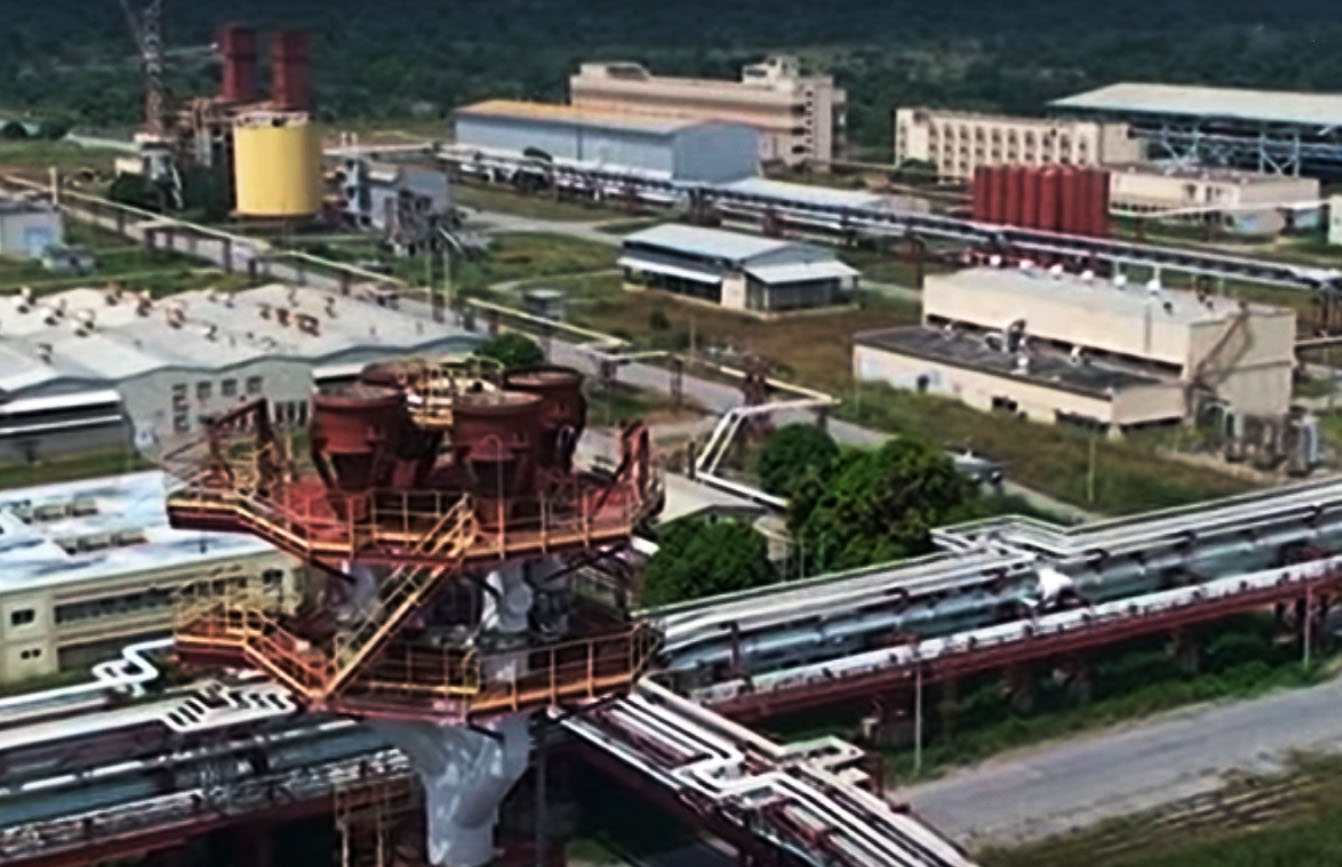
Located in Ajaokuta, Kogi State, Nigeria, it is built on a 24,000 hectares (59,000 acres) site. It is the largest steel mill in Nigeria, and
the coke oven and byproducts plant are larger than all the refineries in Nigeria combined. Other mills in Nigeria are Aladja, Osogbo, Katsina
and Jos rolling mills.
However, it has never produced any steel, and it is non-operational as of December 2018.
Earlier on in 1973, iron ore of the required quality (to make good steel) was discovered in Itakpe, Ajabanoko, and Oshokoshoko. This discovery was the main reason behind commisioning Ajaokuta Steel Company to process the iron ores from Itakpe, Ajabanoko, and Oshokoshoko. However, both projects have been mismanaged. The Ajaokuta Steel Mill has not produced a single sheet of steel after more than three decades, although 40 of the 43 plants at the facility had been completed.
After several failed attempts to privatize both projects, the Nigerian government took back control in 2016. Then Itakpe–Warri Railway fell into disrepair, and part of the track was vandalised. The Nigerian government awarded contracts to the China Civil Engineering Construction Corporation and Julius Berger to repair and complete the railway.
In January 2019, Abubakar Bwari, the Minister of State, Mines and Steel Development, said that 11 companies have indicated interest to operate
the Ajaokuta Steel Company. Mr Bwari also confirms the government plans as for the steel mill as follows "the federal government is not
ready to hand over the company now, as all infrastructure required for the commencement of the company such as rail, dredging of Lokoja and
Warri ports are yet to be completed. He said the company would be handed over to a competent organisation with financial and technical capability,
but preferably a Nigeria company, to manage the steel industry as soon as all infrastructure needed were completed. The policy of the
government is that it will not release Ajaokuta steel just like that; what we are planning to do is to regulate and create enabling
environment for the company to strive."
(source: companies indicating interest to run ajaokuta steel)
Shamefully after 40 years, our government is still playing yoyo with Ajaokuta steel mill - our main potential source of producing steel. The projects to finish off what the Russians started 40 years ago have been awarded over and over to different incompetent individuals and fake companies and still no steel is being produced but billions of naira have disappeared into the pockets of these people.
There is only one thing to do going forward (to avoid further mismanagement and theft of state funds) and that is for the governent of President Buhari to award the contract to finish the mill for a fair, reasonable and competitive price to TPE, the Russian firm that completed the 40 units of the planned 43 units. Current claim by the Chairman, Senate Committee on Mines and Steel Development, Senator Tanko Al-Makura (Dec, 2020) that "to complete the final phase of the Ajaokuta Steel firm, N3 billion will be needed to hire Russian experts to reactivate the 21 plants at the Iron and Steel Industry, looks to be on a very steep side even though it is still unclear how much work is really there to do.
If genuine attempt is not made by the Buhari government to complete or revive the steel mill to full operation by 2023, KETA will complete the three remaining units needed to commence operation. KETA will also expand and modernize the operation of the steel mill to include a new and modern coke oven and casting units. This is because a new and modern mill is actually needed given that this mill built by the Russians are using a technology of more than 40 years old. For Nigeria to embark on any kind of manufacturing and industrial revolution, production of steel and aluminuim would be a must, so it's importance to our future economic survival cannot be over emphasized.
Must Read
- Ajaokuta Steel: How Obasanjo, Jonathan failed Nigeria
In a stunning revelation at the House of Representatives, the administrations of late Gen. Sani Abacha, Olusegun Obasanjo, Goodluck Jonathan and incumbent President Muhammadu Buhari have been blamed for the comatose state of the Ajaokuta Steel Mill. Also allocated blames are Governor of Kogi State, Yahaya Bello, the Economic and Financial Crimes Commission (EFCC), Acting Registrar of Corporate Affairs Commission (CAC), Azuka Abigail and Global Infrastructure Nigeria Limited.
A legal practitioner, Natasha Adeiza made these claims during a sectoral debate on the Ajaokuta Steel Mill on the floor of the House of Representatives on Thursday.
Adeiza stated emphatically that the only reason why the facility is in its current state of disarray is because of a lack of political will by the aforementioned administrations.
She noted that despite several overtures by the Russian Federation, especially through a letter personally written by the President of Russia, Vladimir Putin, were rebuffed, noting in particular that the Obasanjo administration declined the offer from the Russians to help. Instead, the administration conceded the plant to a company with neither the technical expertise nor the financial wherewithal.
She added that Musa Yar’Adua’s administration, through a report by the Jimoh-Mogaji-led committee, ordered for the prosecution of all officials involved in the concession.
However, the EFCC has failed to reopen the case against the indicted officials even after she and other patriotic lawyers offered to work on the case pro bono on behalf of the country.
Adeiza revealed that the former Attorney General, Muhammed Adoke, with the approval of President Goodluck Jonathan, agreed to an out-of-court settlement with a company called Global Infrastructure (Nigeria) Limited (GINL), after the court already struck out a case by the concessioner, and the government still agreed to pay the company the sum of $525million in line with the recommendation from the former Vice President’s (Namadi Sambo) committee.
This led her to question the validity of GINL’s claim, adding that the Central Bank of Nigeria’s records show an unpaid loan by GINL.
The revelations continued as she presented two separate concession agreements. She also alleged that the concession agreement by the current administration is skewed in favour of the concessioner against the interest of Nigerians.
Right here, I have two agreements, one by Adoke and the re-concession one by Fayemi. The two agreements are one and the same, [and] in fact [they have the] same typographical errors,” she said.
Furthermore, Adeiza added that the conspiracy also extended to the current Governor of Kogi State, Yahaya Bello. She disclosed that her investigations showed that the Ajaokuta Limited company, recently registered by the Kogi State Government as a special purpose vehicle to concession the Ajaokuta Steel Company in partnership with Global Infrastructure Limited, favours GINL more.
According to her, the company’s registration was invalidated in lieu of the investigation carried out by the CAC following a petition from her. However, she said another letter from the Acting Registrar of CAC gave the green light to the Ajaokuta Company citing an order from the Presidency.
She disclosed that, after careful scrutiny, the arrangement by Kogi State breached the legality of composition, as the two directors of the company were not from Kogi State and also staff of Global Infrastructure Nigeria Limited.
She noted that the Abacha regime also used the Steel Mill to defraud the nation of over $2b, highlighting a United Nations report showing that $2.5b was withdrawn from the federation account by the regime for a loan repayment to the Russians.
However, the actual amount owned to the Russian Government was about $500m after the loan was renegotiated in a secret deal.
Therefore, she recommended a halt to the concession plan, noting that a facility with the potential for weapon making should not be in the hands of an individual. She urged the government to take full control, while engaging the Russian Federation as a technical adviser.
Source: Order Papers Nigeria. Bakare Majeed – March 2, 2018 (m.bakare@orderpaper.ng, editor@orderpaper.ng )
- ANALYSIS: Ajaokuta: How Nigeria’s largest industrial project failed-
December 26, 2017. Francisca Oluyole and Agency Report, Ajaokuta Steel plant Related News
Ajaokuta Steel Coy: Complete it before concession, Sole Administrator tells FG
Workers see solution to Nigeria’s unemployment problem in steel industry reactivation
Nigeria finally retakes ownership of Ajaokuta steel, Itakpe mining Companies - Fayemi
About 12,000 federal projects abandoned across Nigeria
Nigerian government raises hope on reactivation of Ajaokuta steel firm
The Steel Industry is said to be the backbone of any nation.
The industry serves as stimulus to national development and economic boost to industrial growth of a country.
The Ajaokuta Steel Company in Kogi State of Nigeria was envisaged to serve as the bedrock of Nigeria’s industrialisation.
The idea of having a steel industry was conceived in 1958 by the federal government. Preliminary market studies were carried out and studies were initially directed towards the feasibility of establishing rolling mills. However, because of the growing awareness of the availability of iron ore in Agbaja, Udi and other areas of the country, emphasis later shifted to establishing an integrated steel plant.
Late Tafawa Balewa and late Nnamdi Azikiwe between 1960 -1966 invited and received proposals from foreign firms, including those from UK, U.S., Germany and Canada, most of these being on the feasibility of establishing steel complexes. The efforts of the government did not yield significant positive result because they were based on the use of iron deposits in Agbaja and Udi which were later found to be unsuitable for direct reduction.
In 1967, a team of Soviet experts arrived in Nigeria to conduct a feasibility study on the establishment of an iron and steel plant, as a follow-up on a technical/economic cooperation agreement between the governments of Nigeria and the USSR. In their report, they recommended the use of blast furnace process of iron making. The report also pointed out that the known iron ore deposits in the country were of poor quality and recommended that further geological surveys be conducted to see if better ore could be found. In 1968, Soviet geological experts came to Nigeria and after a general geological investigation reported that there were high prospects for richer iron ore and coal deposits in the country.
However, the federal government signed a contract in 1970 with TYAZHPROMEXPORT (TPE), a Russian company, under which they agreed to provide specialised equipment to carry out further geological survey to determine the quantity of the deposits of iron ore, coal resources in the country that could be used for the proposed iron and steel industry.
By 1973, suitable iron ore deposit was discovered in Itakpe, Ajabanoko and Oshokoshoko all in the region around Kabba-Okene-Lokoja – Koton Karfe axis, now in Kogi State. The TPE was contracted to prepare the preliminary project report for the proposed Iron and Steel Industry in Nigeria.
In 1975, during the reign of Murtala Mohammed, the preliminary project report specifying the raw materials base at Itakpe in Kogi plant site location (Ajaokuta), 1st phase production volume (1.3 mmt), process route (Blast Furnace -Basic Oxygen Furnace), Product form (Long products) submitted by TPE was reviewed, discussed and accepted. TPE was subsequently commissioned to prepare the Detailed Project Report (DPR) on Ajaokuta which was completed and submitted in 1977.
In 1979, Ajaokuta Steel Company Limited (ASCL)/NIOMCO, Delta Steel Company (DSC), among others, were established under Section 2 of National Steel Council Decree No. 60 of September 19, 1979 and incorporated as Limited Liability Companies.
In 1980, former President Shehu Shagari laid the foundation stone of an integrated steel plant in Ajaokuta on 24,000 hectares of sprawling green-field landmass, built on 800-hectares. The steel company has four different types of rolling mills inside the plant, such as the Billet Mill which produces billets; the Light Section Mill which produces round, square, strip and angles metals.
The Wire Rod Mill produces wire rods and rebars used in construction companies and production of nails, fencing wire, rope mesh, bolts and nut and netting and the Medium Section and Structural Mill produces parallel flange channels, equal angles, unequal angles and standard channels. The four rolling mills are bigger than Aladja, Osogbo, Katsina and Jos rolling mills put together while the coke oven and bye products plant is bigger than all the four refineries in Nigeria put together.
In 1980 to 1983, the administration achieved 84 per cent of Ajaokuta steel plant as the Light Section Mill of the plant was commissioned earlier than the scheduled date, while the Wire Rod Mill was also commissioned in April 1984, earlier than the scheduled month of December.
In 1994, equipment erection work at Ajaokuta Steel Plant reached 98 per cent completion.
With all these achievements, it was, however, sad that the gigantic steel plant idea conceived and executed by past leaders had failed to contribute to the development of Nigeria. The Ajaokuta steel that had reached 98 per cent completion as far back as 1994 had not produced a single steel till date.
The integrated plant was envisaged to have multiplier effects on all sectors of the Nigerian economy such as the industrial, agriculture, transport and construction sectors, among others. The steel plant was designed to produce 1.3 million tonnes of liquid steel per annum in its phase one, with a built-in capacity to expand its production to 2.6 million tonnes of flat iron and steel products in its second phase and phase three plan was planned to produce 5.2 million tonnes of various types of steel products, including heavy plates.
The steel plant complex also has highly sophisticated assemblage of 43 different plants made up of a web of complex iron, cable and machinery of different sizes and functions.
Out of the 43 plants, 40 are already completed and can produce independently.
Ajaokuta steel has the capacity to become a major producer of industrial machineries, auto-electrical spare-parts, shipbuilding, railways and carriages. The steel plant’s first phase has the capacity to provide direct employment for 10,000 technical staff and indirect 500,000 for unskilled upstream and downstream employment if it is in operation. The federal government had spent over $10 billion over 34 years and would require another $2 billion to complete the remaining two per cent of the plant. South Korea, which started its steel construction around the same time with Ajaokuta steel now has a revenue base of over 60 billion dollars per annum and employed over 65,000 staff. Ajaokuta steel would have done better if it had started production.
According to World Steel Association (WSA) report, South Africa and Egypt produced 6.1 and 5.0 million tonnes of steel in 2016, while South Africa is the 22nd on the list of countries on steel production, Egypt is the 27th. China, the world’s largest steel producer topped the chart with a production of 808.4 million tonnes representing about 50 per cent of global steel output for 2016, as Japan and India produced 104.8 and 95.6 million tonnes of crude steel to maintain the second and third position on the list. Virtually all the nations that are playing big globally have enhanced capacities for steel production.
Even those that do not have any of the key mineral inputs needed for steelmaking had over the years developed the capacity to produce steel.
Japan and South Korea, for instance, have no mineral resource for iron and steel, but they rank among the world top 10 countries in steel production.
Nigeria that is blessed with raw materials such as iron ore, coal, natural gas and limestones needed for the manufacture of steel is still struggling with what to do with the dormant plant.
In June 2003, former President Olusegun Obasanjo conceded Ajaokuta steel to Messrs SOLGAS ENERGY of USA on a 10-year tenure; in August 2004, the Federal Government terminated the SOLGAS Agreement due to non-performance. In 2004 and 2005, the Obasanjo administration, again, granted another concession to Global Infrastructure Nigeria Limited (GINL) an India company for the operation of Ajaokuta steel and the Nigeria Iron Ore Mining Company (NIOMCO) at Itakpe in Kogi. However, the Indian company did not live up to federal government’s expectation in managing the two companies.
Consequently, the late Umaru Yar’Adua administration was compelled to revoke the contract in April 2008 without meeting the requirements of the clauses built into the agreement. The Indian company thereafter took Nigerian government to arbitration court in London, which also crippled the two firms.
In 2016, President Muhammadu Buhari fulfilled his campaign promise on Ajaokuta steel by settling the legal bottleneck surrounding the companies out of court. However, the federal government signed modified concession agreement with GINL to enable the firm to retain the National Iron Ore Mining Company, Itakpe.
The modified seven-year concession agreement was signed on August 1, 2016, while the federal government took over the Ajaokuta steel.
While the federal government was planning to reconcession Ajaokuta steel again, stakeholders in the Nigerian Metallurgical Society urged it to complete the remaining two per cent and operate the plant for few years before concessioning it.
Source: https://www.premiumtimesng.com/news/headlines/253680-analysis-ajaokuta-nigerias-largest-industrial-project-failed.html
- President Buhari Rejected the $1BN Ajaokuta Completion Fund Bill-
President Muhammadu Buhari has refused assent to the bill seeking for $1 billion for the completion of Ajaokuta Steel Company.
The rejected bill with seven others were forwarded to him by the National Assembly in February this year.
In separate letters read on the floor of the Senate Tuesday by the Senate President, Bukola Saraki, Buhari cited several reasons ranging from infractions on extant laws, duplication of responsibilities of existing agencies, to financial constraints for refusing assents on the bills.
The President in his refusal to sign the Ajaokuta Completion Fund Bill as stated in a letter dated March 19, 2018, said appropriating $1billion from the Excess Crude Account ( ECA) as requested for in the bill by the federal lawmakers is not the best strategic option for Nigeria at this time of budgetary constraints.
He said: ” The Nation cannot afford to commit such an amount in the midst of competing priorities with long term social and economic impact that the funds can be alternatively deployed towards.
“Bills which seeks to make an appropriation of revenues to fund public expenditure should be consolidated in the annual Appropriation Act such that these proposals pass through the traditional scrutiny that budget proposals are subjected to by the Ministry of Finance, Ministry of Budget and National Planning and the National Assembly.
“Furthermore, as the Excess Crude Account Funds belong to the Federation, it would be proper to consult with the National Economic Council where the States are represented.
“Relevant stakeholders such as the Ministries of Mines and Steel Development, Industry, Trade and Investment were not fully consulted.
“The inputs of key stakeholders are necessary to create the optimal legal and regulatory framework as well as an institutional mechanism to adequately regulate the steel sector ”
In another letter of refusal of assent dated March 27, President Buhari cited provisions contained in section 32 of the Small and Medium Enterprises Development Agency Bill 2018 as the major reason for refusing assent to it.
He said, “Section 32 of the Bill , introduces (I) a 2.5% levy on the profit before tax of the target companies which will increase the tax burdens of the companies while offering no direct benefit to them : (ii) a1% levy on imports which will also add to the cost of doing business in the country , (iii), a 5% levy on luxury goods which duplicates efforts by the Federal Ministry of Finance to raise excise on such goods in a more sustainable manner to the benefit of the Federal Government treasury “.
He added that if signed into law, the Agency will have similar objectives to the Bank of Industry particularly with regard to the funding of Small and Medium Enterprises.
“Accordingly, it is important to streamline its functions to avoid duplication or overlap of functions with other government institutions performing similar functions aside from the likelihood of increasing public recurrent expenditure by the proposed creation of new public sector bodies “.
Other bills declined assents by the President through separate letters forwarded to that effect to the Senate are, the Nigerian Aeronautical Search and Rescue Bill 2018, Chartered Institute of Training and Development of Nigeria ( Establishment) Bill 2018 and Federal Mortgage Bank of Nigeria Bill 2018.
Others are, the National Housing Fund Bill 2018, National Institute of Credit Administration Bill 2018 and National Bio-Technology Development Agency Bill 2018.
Source: https://dailypost.ng/2019/04/02/buhari-declines-assent-bill-seeking-1bn-completion-ajaokuta-steel-company-l7-others/
- Natasha Akpoti exposes conspiracy on Ajaokuta Steel
- Ajaokuta Steel Company
Source: Odinaka Anudu, April 8, 2019
Last week, Nigeria’s President Muhammadu Buhari rejected the Senate-proposed $1 billion for the revival of Ajaokuta Steel Complex in a bill now known as Ajaokuta Steel Company Completion Fund Bill.
In a synopsis, Buhari said he rejected the bill, among others, because appropriating $1 billion from the Excess Crude Account to Ajaokuta was not ”the best strategic option for Nigeria at this time of budgetary constraints, and the nation cannot afford to commit such an amount amid competing priorities.”
He further said that the Excess Crude Account belonged to the federation so it was necessary to consult with the National Economic Council and the states. He added that the most critical ministries, notably the Ministry of Mines and Steel Development, and the Ministry of Industry, Trade and Investment were not fully consulted.
“The inputs of key stakeholders are necessary to create the optimal legal and regulatory framework as well as the institutional mechanism to adequately regulate the steel sector,” he said.
The question now is, was the president right in taking this decision?
To answer this question, it is critical to note that Ajaokuta Steel was established in 1971 to develop Nigeria’s steel sector and stimulate the exploration of God-given natural resources, especially iron ore. Luckily for the country, large iron ore deposits were found in Itakpe, Ajabanoko and Oshokoshoko all in Kogi State. The Ajaokuta Steel Complex and Delta Steel Company were subsequently incorporated in 1979 as limited liability companies.
It was also widely reported that erection work on equipment reached 98 percent completion around 1994. Ever since then, Nigerians have been made to believe that Ajaokuta is 98 percent completed.
But here lies the biggest puzzle: Why is a company that is 98 percent completed still failing to produce a sheet of steel over 35 years after its establishment?
Despite being unproductive, government after government has continued to pump billions into the complex. Government records show that successive administrations have pumped $8bn so far into the complex since 1979. The current government of Muhammadu Buhari has joined the party of spenders on a government facility that needs to be in private hands.
In a move that shocked economists and finance experts, the federal government budgeted N3.9 billion in 2016 and N4.27 billion in 2017 for the resuscitation of the moribund Ajaokuta Steel Company, despite an earlier business case in the last administration showing that the complex could only work if properly privatised. There was also a humongous budget on it in 2018.
“So why would anyone continue to pump money into an enterprise that is unproductive?” Ike Ibeabuchi, a manufacturer, asked. “The government says new investors are interested in taking over the complex, so why would Nigeria spend that huge fund on it?”
Eleven private investors have expressed interests in the concessioning of Ajaokuta Steel Company, Abubakar Bawa Bwari, minister of mines and steeldevelopment, said in the nation’s capital on January 15.
Bwari said it would be concessioned to a firm with the financial muscle, technical know-how and genuinely committed to the nation’s steel sector development.
“But then, why have they not found investors since Kayode Fayemi’s days? We don’t know whether this so-called Ajaokuta is meant for siphoning public funds,” a private sector player in the steel sector, who does not want his name in print, said.
Ajaokuta Complex has the capacity to produce one million metric tonnes of steel, one million metric tonnes of coal , manganese and limestone, among others, but it is yet to produce a sheet. It has a managing director and staff members who are paid from tax payers’ funds.
“Currently, I am not sure those technologies at Ajaokuta are competitive in steel making. The world has moved on. What is required now is for the private sector to get more and more involved in the downstream and the upstream segments in the steelbusiness,” Raj Gupta, chairman, African Industries Group, a consortium of 12 companies, including six steel plants, told BusinessDay recently.
This shows that it makes no sense to continue to allocate scarce resources to a complex which is unproductive. Analysts say the best bet now is to sell it to a competent firm, just like Delta Steel has been sold to Premium Steel.
BusinessDay’s recent visit to Premium Steel showed that the company employs 160 workers in its rolling mill, which is the only functional section at the moment. There is also a plan in place to revive other sections of the factory with N600 billion.
Moreover, as Buhari stated, Nigeria is a cash-strapped economy struggling to pay its workers and meet infrastructure obligations. Federal allocation to states was N660.37 billion in February as against N1.19 trillion in August 2013. Industry analysts believe that Buhari was right to reject the bill and urge him to privatise it as soon as possible, while stopping allocations to it.
Nigeria’s only aluminium smelting plant, ALSCON, (in Ikot Abasi was launched in 1997) with a total annual capacity of 200,000 tonnes per year was shut down in 2014 following crippling protests embarked upon by the company’s staff against poor working conditions, dwindling productivity and spiralling debts.
The management of ALSCON, Russian aluminium giant, United Company RUSAL PLC, dismissed almost all local personnel of its workforce.
As at May 2018, the smelter is still not in operation as the youths under the aegis of Ikot Abasi Clan Youth Leaders Forum expressed fears that almost six months after RUSAL, a Russian company and BFIG Company settled out of court over bidding matter, nothing was happening at ALSCON.
According to the Nigerian government (Minister), government now owns a minority 20 percent of the smelter, Rusal 80 percent, the minister said. These numbers were disputed by Rusal whose spokesperson said the company retained 85 percent and Nigeria 15 percent. (https://rusal.ru/en/about/51/)
While aluminium is not the strongest metal, alloying it with other metals helps to increase its strength. Its corrosion resistance is an added bonus, eliminating the need for heavy and expensive anti-corrosion coatings (needded in other metals like steel)
Aluminum is produce from bauxite in two major stages:
1. -Alumina (aluminum oxide), a white, granular substance which looks somewhat like sugar, is refined from bauxite in a several-step caustic soda/high temperature process.
2. -The alumina is electrolytically reduced in molten cryolite to separate it into aluminum and oxygen.
Today, aluminium is the second most used metal in buildings after steel. Because of its ductility, aluminium can be formed into many
shapes and profiles, e.g. aluminium wall cladding systems are commonly used for building exteriors, with large wall panels requiring fewer
joints, resulting in time-efficient installation
Countless objects that simplify as well as increase the quality of our daily life are fully or partly made of aluminum, For example:
CDs, cars, engines, refrigerators, kitchenware, electric power lines, packaging for food and medicine, computers, furniture and aircrafts.
We also use aluminum every day in many things we use and we don't often realize it.
By now it should be clear that aluminium is a must have in any industrialized economy. That is why it is essentially important that we produce our own aluminium, and that means that we have to mine (bauxite and other metal ore) and produce aluminium by building our own aluminium smelters.
Again like Ajaokuta (steel mill) built by the Russians, the technology used in ALSCON is probabaly old. There are modern and new technologies and smelting techniques better than the one used by the Russians.
Source:
By TODAY -January 21, 2018
The Federal Government has given official recognition to Messrs UC Rusal, a Russian Company, as the core investor of the Aluminium Smelter Company of Nigeria (ALSCON), Ikot Abasi, Akwa Ibom State, following the signing of the Renewed Share Purchase Agreement between Government and the Russian company in Abuja, on Friday.
The Renewed Share Purchase Agreement, was signed during a brief ceremony at the Ministry of Mines and Steel Development, Abuja, witnessed by the Minister, Dr Kayode Fayemi; Minister of State, Hon Abubakar Bawa Bwari; Director General, Bureau of Public Enterprise (BPE), Alex Okoh; Russian Ambassador to Nigeria, Nickolai Udovichenko; CEO/Member of the Board of Directors UC Rusal, Vladislav Soloviev; Managing Director ALSCON, Dmitry Zavyaiov; and Head of Legal, UC Rusal, Piter Maxsimov.
Director General BPE, Alex Okoh, signed for the Federal Government, while CEO/Member of the Board of Directors UC Rusal, Vladislav Soloviev, signed on behalf of the company, thus ending the protracted litigation that has made the aluminium smelting company unable to operate for almost a decade.
The Federal Government, however, still retains 20 per cent equity in the company.
Government took the decision to intervene and end the protracted dispute at the meeting of the National Council on Privatization (NCP) held in August, 2017 under the chairmanship of the Vice President, Prof Yemi Osinbajo, where Council approved an out of court settlement to resolve the lingering dispute between the FGN, BFIG AND UC RUSAL through mediation with the active collaboration of Ministry of Mines and Steel Development.
Speaking at the event, Dr Fayemi stated that President Mohammadu Buhari is keen on seeing that this agreement is reached and resolved as soon as possible so that the company can get back on its feet and Nigeria and Russia can strengthen the historical partnership btw the two countries.
The DG of BPE, Okoh, in his remarks commended the efforts of the Minister of Mines and Steel Development, Dr Fayemi, and his commitment in ensuring the success of the negotiation.
The BPE boss said he is optimistic that the remaining issues would be resolved both on the legal side as well the technical and production issues, adding that government still retained 20 per cent equity in the firm.
Ambassador Nickolai Udovichenko who led Russian Government delegation to the event, thanked the Nigerian Government for resolving the impasse, while also lauding the efforts of the Minister.
He described the development as a new beginning for the two countries.
Source:
By News Agency of Nigeria -June 28, 2018
Abubakar Bwari, the Minister of State, Mines and Steel Development, says the Aluminum Smelter Company of Nigeria (ALSCON) in Ikot Abasi in Akwa Ibom would resume production soon.
Mr Bwari gave the assurance while receiving the Russian Ambassador to Nigeria, Alexey Shebarshin, who paid him a courtesy visit on Thursday in Abuja.
According to him, ALSCON which has been moribund for over a decade will soon be put to use.
The minister said that Messrs UC Rusal, a Russian company which finally won the bid for the company had already submitted a business plan to the Bureau of Public Enterprise (BPE) adding that the company is also working on plans to commence technical audit of the plant.
According to him, the Federal Government is making effort to ensure that the Ajaokuta Steel Company (ASC) also comes on board soon.
He said that Nigeria has a long standing bilateral relationship with Russia, adding that Russia has great connections with the formation and construction of the ASC.
The News Agency of Nigeria (NAN) reports that the Federal Government had launched a technical audit to find out requirements for the completion of the company at the end of which an estimated $652 million was recommended for its reactivation.
Mr Bwari commended the ambassador, for the visit which took place barely a month after he assumed office in Nigeria.
“We are happy to receive the ambassador because our ministry is the second ministry he has visited; he visited the Ministry of Agric first and he has barely spent a month in Nigeria as the Russian ambassador,’’ he said.
Earlier, Mr Shebarshin said his visit was to strengthen existing bilateral relationship between Russia and Nigeria on mining exploration and other areas.
He advised the minister to make contact with JSC Zarubezhgeologia, a Russian company in his efforts to revive the ASC and make it operational.
Mr Shebarshin said JSC Zarubezhgeologia was an exploration company between 1969 and 1983 in Nigeria, adding that the ministry can partner with the ministry on geological issues and mineral exploration.
NAN recalls that the Russian company had to its credit the discovery of large deposit of dolomite, iron ore, lime stones and other minerals in Kogi, which prompted the Federal Government to set up the Ajaokuta Steel Company.
Source: By News Agency of Nigeria -June 28, 2018
Looking in from outside, it is not possible to really and fully understand what has gone wrong or is still going wrong with ALSCON except that when
one is in the government then the ALSCON story will become clearer but whatever the situation is in 2023 KETA will commit to ensuring that ALSCON is
completed by the Russians and put into operation. KETA will then build a new aluminium smelter using the world latest technology to increase
our production capacity of this great metal. Also because huge amount of power is needed during the seperation of oxygen from alumina to produce
aluminium, we will have to build separate power generators to service the smelters.
While there will be an initial focus on the development of a couple of industries to facilitate a gradual move to industrialization at the beginning, different industries will be developed simultaneously. The most important of these industries will be the energy industries, specifically the generation, transformation and the distribution of power.
Adequate attention will be given to the manufacturing of electrical parts and components used in the generation, transformation and distribution of electricity. This is to enable quick servicing and relatively easy maintainance in these industries as well as helping to reduce the level of power outage.
Once an acceptable level has been achieved in sustainable manufacturing of servicing parts and components, our main focus will shift to the actual generation and distribution of energy. Within eight years, KETA government will ensure that we generate, transmit and distribute atleast 200,000MW of electricity. Within the first four years of our industrial revolution, KETA governement will ensure that as much as 100,000MW of electricity is generated, transmitted and distributed through out the country. Even with a substantial increase in economic activities, 100,000MW is more than adequate to ensure a 24/7 supply of electricity in the whole of Nigeria.
In this interactive audio session which took place over four days (4 parts) we discussed how adequate, consistent and reliable supply of electricity is desperately needed in Nigeria. We then explained how to Generate, Transmit & Distribute 100,000 MW of electricity in 4 years based on our plan to help Nigeria become a manufacturing & an industrialised economy.
Part 1
In this part 1 we discussed:
- Present situation with electricity
- Role of steel & other metals in electricity
supply & industrialisation of Nigeria.
- Present situation with Ajaokuta steel complex,
present situation with Delta steel, ALSCON
& others and how to revive them.
Part 2
In this part 2 we discussed, among others:
- Importance of steel, aluminium and copper in
providing adequate electricity.
- How it will be possible to achieve 100,000 MW
in 4 years.
Part 3
In this part 3 we discussed, among others:
- How much electricity generation, transmission and
distribution planned for each state and the FCT.
- Energy generation mix of fossil fuels (like petroleum,
coal, natural gas, hydrogen, methane, etc) and renewable
energy sources (like hydro, solar, wind turbines, etc).
Part 4
In this part 4 we discussed, among others:
- Continuation: Energy generation mix of fossil fuels
(like petroleum, coal, natural gas, hydrogen,
methane, etc) and renewable energy sources
(like hydro, solar, wind turbines, etc).
- Present and planned future role of GENCO, TRANCO &
DISCO companies, the NBET, system operators, the NERC
& the ministry of power.
- Financing the plan.
Present and Forecast (2027)
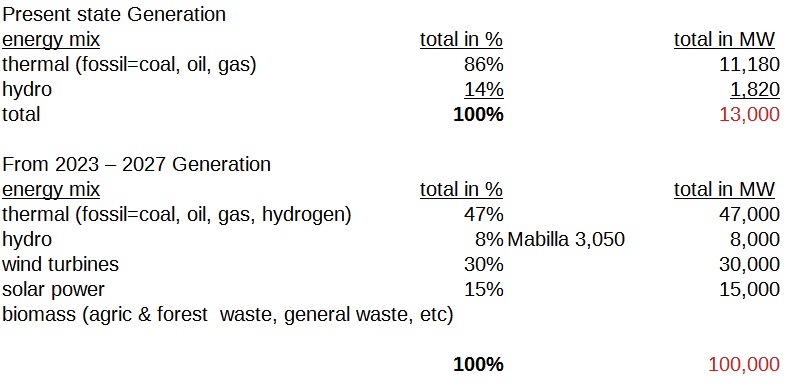

Proposed electricity generation per state :
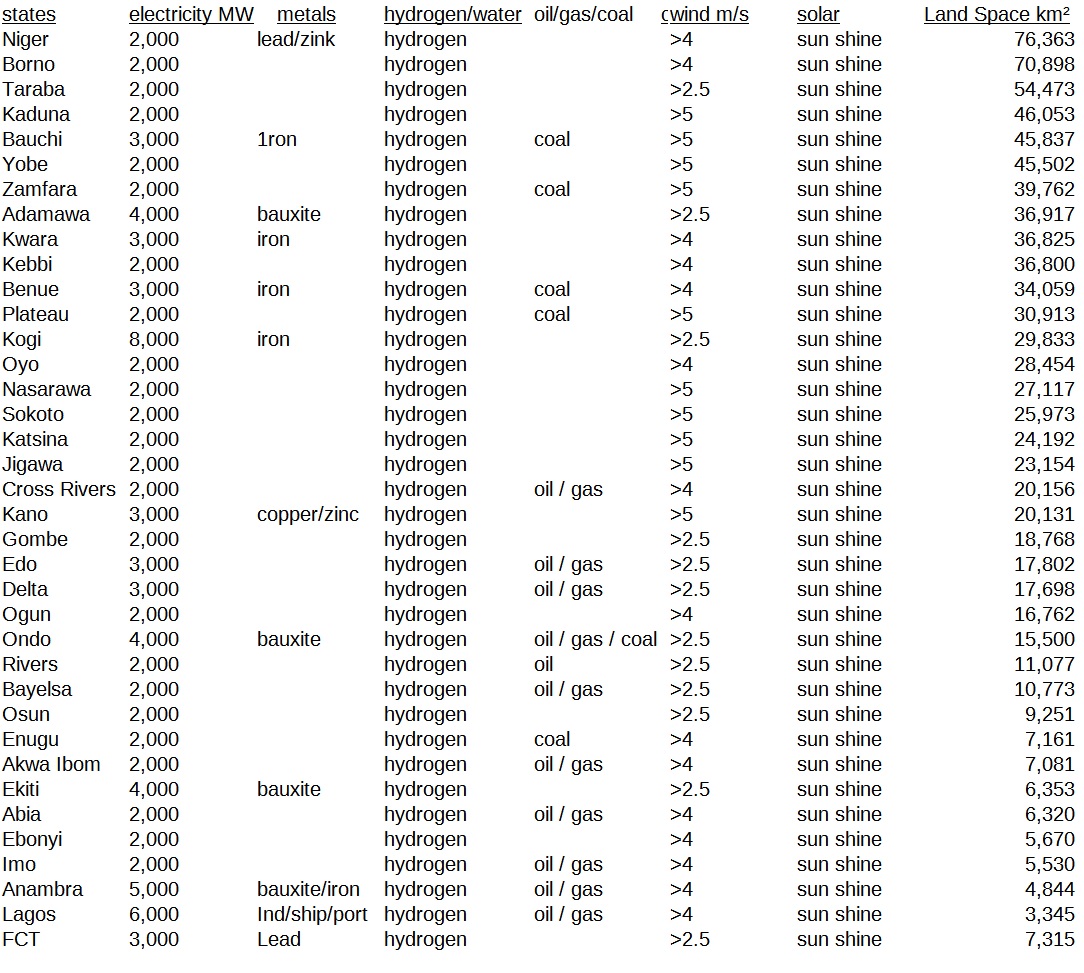
Download:
Energy Options for Sustainable Economic Growth in Nigeria: Status, Issues and the Way Forward
- (the broken promise)
Details of how we can and how we are going to make this happen will be posted here later. Coming soon!
So, if others can, why can't we?
Details of how we can and how we are going to make this happen will be posted here later. Coming soon!
So, if others can, why can't we?
Details of how we can and how we are going to make this happen will be posted here later. Coming soon!
So, if others can, why can't we?
Details of how we can and how we are going to make this happen will be posted here later. Coming soon!
(Cut your coat according to your size)
So, if others can, why can't we?
Details of how we can and how we are going to make this happen will be posted here later. Coming soon!
So, if others can, why can't we?
Details of how we can and how we are going to make this happen will be posted here later. Coming soon!
So, if others can, why can't we?
Details of how we can and how we are going to make this happen will be posted here later. Coming soon!